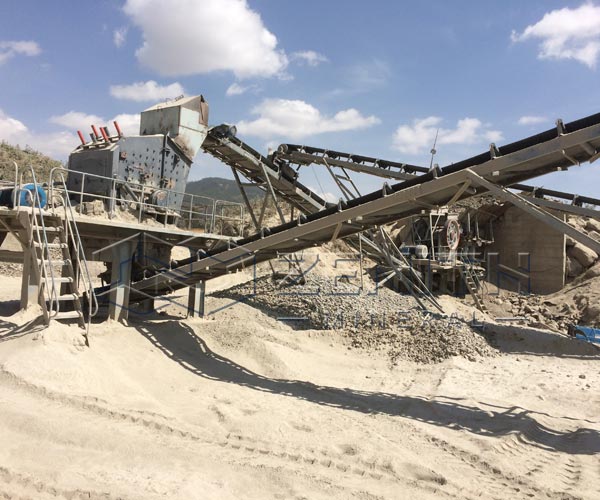
Ethiopian Geology and Mineral Resources: A Crucial First Step
Ethiopia possesses diverse geology with significant potential for exploration and development of various minerals. The country is rich in metallic minerals like gold, platinum, iron, and base metals, as well as fertilizer raw minerals, gemstones, energy minerals, cement raw minerals, ceramics raw minerals, glass raw minerals, and dimension stones like marble and granite. Understanding the specific characteristics of granite deposits in Ethiopia is crucial for tailoring the crushing production line to the local resources.
Assessing the Client’s Specific Requirements and Output Goals in Ethiopia
Before designing the production line, it’s essential to understand the client’s specific needs, including:
- Desired Output Capacity: Determine the required output capacity of the production line (e.g., 2000 tons per hour) to meet the client’s production goals.
- Product Types and Specifications: Identify the desired product types and specifications, such as the required sizes of sand and gravel (e.g., 0-4.75mm sand, 4.75-10mm gravel, 10-20mm gravel, and 20-31.5mm gravel).
- End-Use Applications: Understand the intended applications of the produced granite (e.g., concrete aggregate, road construction) to determine the necessary quality and grading requirements.
Selecting the Appropriate Crushing Process and Equipment for Ethiopian Granite
- The selection of the crushing process and equipment is critical for achieving the desired output and product quality. A typical granite crushing production line involves multiple stages:
- 1. Coarse Crushing: Jaw crushers are commonly used for the primary crushing stage to reduce the raw granite ore to a manageable size. For a high-capacity production line (e.g., 2000 t/h), multiple jaw crushers may be required.
- 2. Medium and Fine Crushing: Cone crushers are typically employed for secondary and tertiary crushing to further reduce the granite particle size. Hydraulic cone crushers are often preferred for their efficiency and ability to handle hard materials like granite.
- 3. Shaping: Vertical shaft impact crushers (VSI crushers) can be used for shaping the crushed granite particles to improve their form and meet specific application requirements.
- 4. Screening and Washing: Screening equipment is used to separate the crushed granite into different size fractions, while washing equipment removes impurities and dust to improve the product quality.
Optimizing the Plant Layout and Flow for Efficiency in the Ethiopian Context
The layout of the crushing plant and the flow of materials are crucial for maximizing efficiency and minimizing operational costs. Consider the following factors when designing the plant layout:
- Proximity to Granite Source: Locate the crushing plant near the granite quarry to minimize transportation costs.
- Material Handling: Implement an efficient conveying system (e.g., belt conveyors) to transport materials between different crushing stages and workshops.
- Workshop Arrangement: Organize the main crushing workshops (coarse crushing, medium and fine crushing, shaping) and screening/washing workshops in a logical sequence to optimize material flow.
- Storage and Stockpiling: Provide adequate storage areas for raw materials, semi-finished products, and finished products.
Addressing Environmental and Sustainability Concerns in Ethiopia
It is important to consider the environmental impact of granite quarrying and crushing operations. Implement measures to mitigate dust emissions, noise pollution, and water usage[4]. Consider using a semi-dry process with a tower-like sand-making system to reduce water consumption.
Complying with Ethiopian Regulations and Standards
Ensure that the design and operation of the granite crushing production line comply with all relevant Ethiopian regulations and standards related to mining, environmental protection, and worker safety.
The Importance of Local Expertise and Collaboration in Ethiopia
Collaborating with local experts and businesses in Ethiopia is crucial for the success of the project. Local partners can provide valuable insights into the geological conditions, regulatory environment, and market dynamics. They can also assist with equipment installation, maintenance, and workforce training.