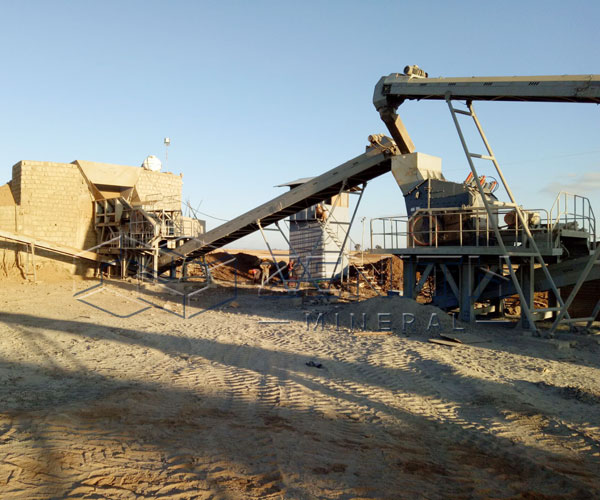
Ethiopia’s construction and mining industries are experiencing growth, creating opportunities for stone crusher plants that produce aggregates for building and infrastructure projects. This guide provides a step-by-step approach to starting a stone crusher plant business in Ethiopia.
Conducting Market Research and Identifying Opportunities in Ethiopia
Before investing, it is important to understand the demand for crushed stone products in specific regions of Ethiopia. Construction projects, road development, and urbanization drive the need for aggregates. Identifying areas with high construction activity or infrastructure development plans can reveal potential business opportunities.
Developing a Comprehensive Business Plan Tailored for the Ethiopian Market
A detailed business plan is essential for success. It should include:
- Executive Summary: A brief overview of the business concept, mission, and objectives.
- Market Analysis: An assessment of the demand for crushed stone, the competitive landscape, and target customers.
- Products and Services: Define the types of crushed stone products the plant will offer (e.g., different sizes and grades of aggregates).
- Production Process: Describe the crushing process, equipment to be used, and production capacity.
- Location and Infrastructure: Specify the location of the plant, considering factors like proximity to raw materials, transportation infrastructure, and utilities.
- Marketing and Sales Strategy: Outline how the business will attract and retain customers.
- Management Team: Introduce the key personnel and their expertise.
- Financial Projections: Include startup costs, revenue forecasts, and profitability analysis.
- Funding Request: If seeking external funding, specify the amount needed and how it will be used.
Securing Necessary Licenses and Permits for Operating a Stone Crusher Plant in Ethiopia
Starting a stone crusher plant requires obtaining the necessary licenses and permits from Ethiopian authorities. This may include:
- Mining License: Required to extract raw materials from a specific mining area.
- Environmental Permits: To ensure compliance with environmental regulations.
- Business License: To legally operate the stone crushing business.
- Crushing Plant Operating License: A permit to operate the crushing plant.
Selecting a Suitable Location for Your Stone Crusher Plant
The location of the stone crusher plant is critical for operational efficiency and cost-effectiveness. Consider the following factors:
- Proximity to Raw Materials: Locate the plant near a reliable source of stone or rock.
- Transportation Infrastructure: Ensure easy access to roads or railways for transporting raw materials and finished products.
- Utilities: Availability of water and electricity supply.
- Land Availability and Cost: Secure a site that is large enough for the plant and storage of materials, at a reasonable cost.
Procuring and Installing the Right Stone Crushing Equipment
Selecting the right equipment is crucial for efficient and cost-effective production. Types of crushers include:
- Jaw Crushers: Used for primary crushing of large rocks.
- Impact Crushers: Suitable for crushing medium-hard rocks and recycling materials.
- Cone Crushers: Used for secondary and tertiary crushing to produce finer aggregates.
- Mobile Crushers: Portable plants that can be moved to different locations.
Consider the capacity, efficiency, and maintenance requirements of each type of crusher before making a purchase.
Sourcing Raw Materials for Stone Crushing in Ethiopia
The primary raw material for a stone crusher plant is stone or rock. Sourcing options include:
- Operating a Quarry: Acquiring a mining license to extract stone from a designated area.
- Purchasing from Existing Quarries: Buying raw materials from established quarry operators.
- Recycling Construction Waste: Processing demolition waste and construction debris into usable aggregates.
Implementing Efficient Production Processes and Quality Control Measures
Efficient production processes are essential for maximizing output and minimizing costs. Implement the following:
- Material Handling: Use loaders, conveyors, and other equipment to efficiently move materials through the plant.
- Crushing Operations: Optimize crusher settings to produce the desired aggregate sizes and shapes.
- Screening and Sorting: Use screens to separate aggregates by size and remove impurities.
- Quality Control: Regularly test the quality of the finished products to ensure they meet industry standards.
Marketing and Selling Your Stone Products in the Ethiopian Market
Effective marketing and sales strategies are essential for securing customers and generating revenue. Consider the following:
- Target Customers: Identify potential customers, such as construction companies, road contractors, and government agencies.
- Pricing Strategy: Set competitive prices based on production costs, market demand, and competitor pricing.
- Distribution Channels: Establish efficient distribution channels to deliver products to customers.
- Promotion: Utilize advertising, networking, and direct sales to promote the business.
Managing Finances and Ensuring Profitability in Your Stone Crushing Business
Effective financial management is crucial for the long-term success of the stone crushing business. Key considerations include:
- Cost Control: Monitor and control production costs, including raw materials, labor, utilities, and maintenance.
- Pricing: Implement a pricing strategy that ensures profitability while remaining competitive.
- Inventory Management: Manage inventory levels to meet customer demand without incurring excessive storage costs.
- Financial Reporting: Regularly track and analyze financial performance to identify areas for improvement.
Overcoming Challenges and Ensuring Sustainability in the Ethiopian Context
Starting a stone crusher plant in Ethiopia can present unique challenges:
- Access to Land: Securing land for the plant and quarry operations can be difficult.
- Infrastructure Limitations: Inadequate infrastructure, such as roads and power supply, can increase operating costs.
- Regulatory Compliance: Navigating the regulatory environment and obtaining necessary permits can be time-consuming.
- Community Relations: Maintaining positive relationships with local communities is essential for social license to operate.